Die Ermittlung und Anwendung von Variantenkosten wird oft gescheut, weil sie buchhalterisch schwer abzubilden sind. Dabei könnten sie pragmatisch und effizient durchgeführt werden, ohne die aktuellen Buchhaltungs-Systeme zu verändern.
Üblicherweise werden bei der Entwicklung von Bauteilen und Produkten Investitionen und Bauteilkosten berücksichtigt. Alle weiteren Aufwände, die während der Produktlebensdauer entstehen, werden gleichmäßig auf alle Bauteile aufgeschlagen, um sie bei der Kostenkalkulation zu berücksichtigen.
Bei geringer Produktkomplexität mag dies eine ausreichende Basis für Entscheidung bieten. Bei hoher Komplexität jedoch führen unberücksichtigte Variantenkosten schnell zu Fehlentscheidungen. Falls sich dann die erwarteten Kostensenkungen nicht in der Bilanz widerspiegeln, wird der Kostendruck weiter steigen und zu noch hektischerer Kostensenkung und damit zu noch höherer Komplexität führen.
Ein Teufelskreis, an dessen Ende die Organisation an ihrer Komplexität erstickt und keine Luft mehr für Qualitätsarbeit und Innovationen bleibt. Das muss aber nicht passieren, denn Variantenkosten können ausreichend genau einfach ermittelt und in Entscheidungen berücksichtigt werden:
Inhalt:
Variantenkostenrechnung (VKR)
Da es so einfach ist, werden die Produkt-Kosten meist dadurch berechnet, dass den direkten Kosten die indirekten Kosten gleichmäßig aufgeschlagen werden.
Beispiel: Bei der Produktion von drei Produkten fallen die folgenden Kosten an:
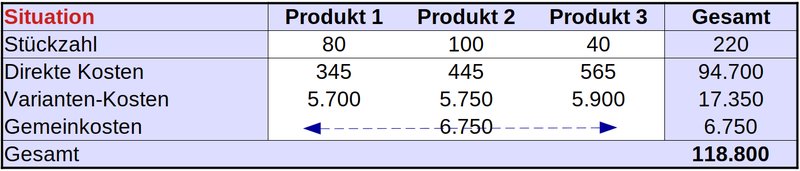
Varianten- und Gemeinkosten werden nicht getrennt, sondern gemeinsam als Indirekte Kosten erfasst. Der Anteil von 24.100€ der Indirekten Kosten entsprechen 25% der direkten Kosten von 94.700€.
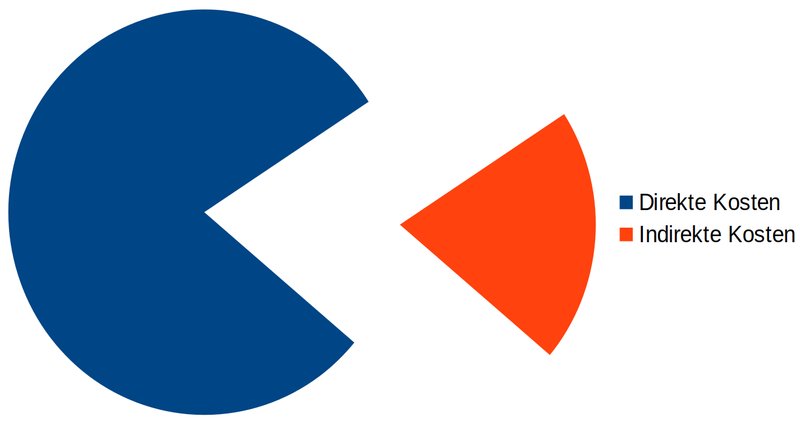
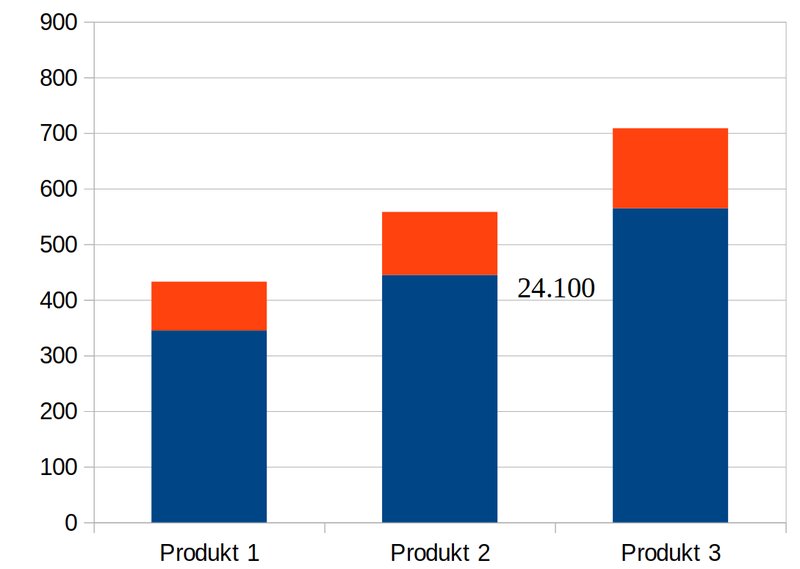
Zur Kostenberechnung erhält jedes Produkt einen Aufschlag von 25% zu seinen direkten Kosten. Das heißt, je teurer ein Produkt ist, desto höher ist der absolute Aufschlag (im Beispiel zwischen 88€ und 144€), unabhängig von seinen Stückzahlen.

Wenn die Variantenkosten auf die Stückzahl der einzelnen Produkte umgelegt würde, wäre der Kostenanteil, der mit „der Gießkanne“ verteilt wird wesentlich kleiner, die Kostenrechnung würde die tatsächlich verursachten Kosten wesentlich genauer widerspiegeln:
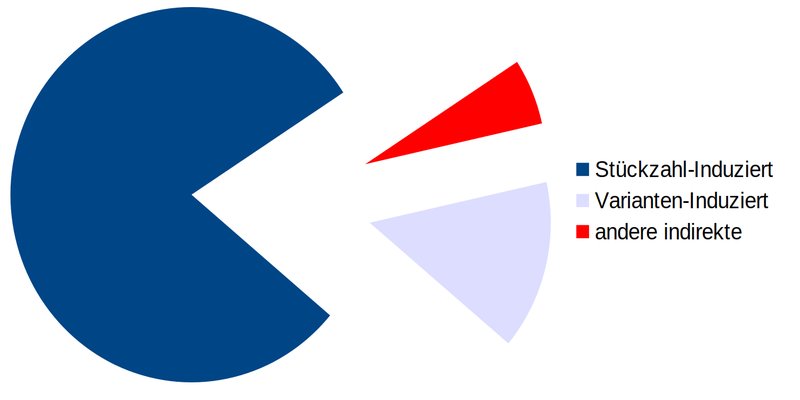
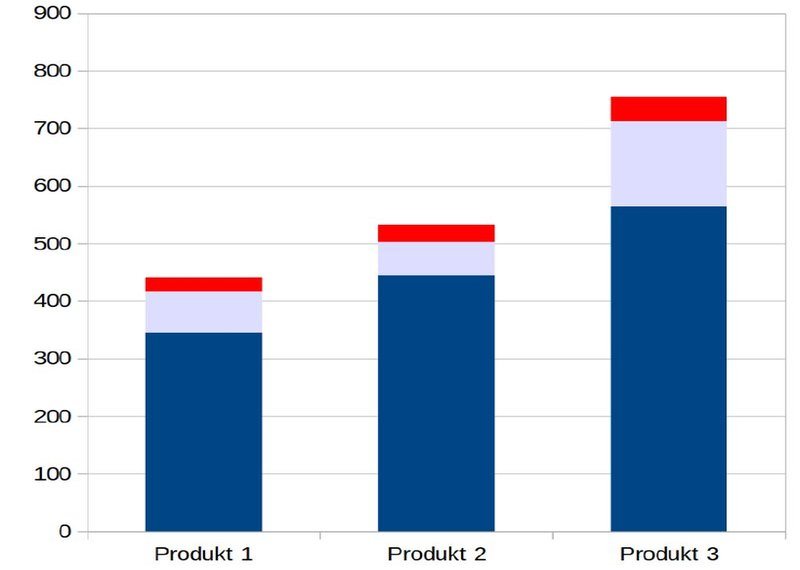
Es wird deutlich, dass die Kostenrechnung ohne Variantenkosten Produkte mit kleinen Stückzahlen bevorzugt, diese werden von den teureren Produkten subventioniert:
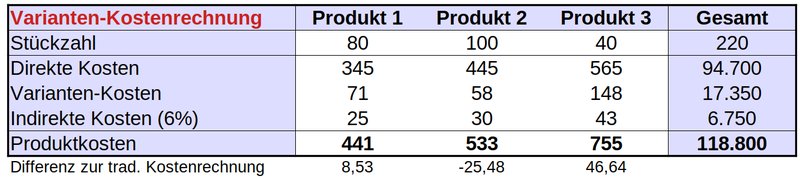
Die Konsequenzen von falschen Produktkosten sind mögliche Fehlentscheidungen, betrachten wir z.B. .
Einführung einer verbilligten Variante
Eine einfache Möglichkeit, bei einem Produkt die Kosten zu senken, ist die Eliminierung von Features, die in einem Teil des Segments gar nicht nachgefragt werden:
Im Beispiel spalten wir Produkt 1 in eine um 40€ verbilligte Variante 1a auf:

Durch die neue Variante erhöhen sich jedoch die Variantenkosten um 3.900€ und die bisherige Stückzahl wird zwischen den beiden Varianten aufgeteilt.
Bei traditioneller Kostenrechnung sind die zusätzlichen Variantenkosten anfangs in der Buchhaltung gar nicht sichtbar, der Verteilungsschlüssel steigt ganz leicht auf 26% an, da die direkten Kosten leicht sinken. Die traditionell kalkulierten Produktkosten wären dann:

Der Gesamtaufwand der Firma sinkt also um die erwarteten 1600€ (40€ * 40Stk), Produkt 1a wird jedoch durch die Kostensenkung von 40€ um 49€ billiger, während die unveränderten Produkte alle teurer werden, da sie den höheren %-Satz der indirekten Kosten abbekommen.
Die zusätzlich generierten Variantenkosten werden erst in den kommenden Jahren als zusätzliche indirekte Kosten sichtbar, die dann wieder % auf alle Produkte verteilt werden, so dass auch hier wieder alle Produkte „teurer“ werden:

Da die indirekten Kosten gestiegen sind, ergibt sich jetzt kein Gewinn mehr für die Firma, sondern eine Kostenerhöhung von 2.300€.
Eine fatale Entwicklung, weil jetzt Produkt 1a signifikant zu billig verkauft wird und womöglich eine noch höhere Stückzahl bekommt, während alle anderen Produkte unnötig teuer verkauft werden und dadurch vermutlich Stückzahl und Deckungsbeitrag verlieren.
Wäre schon bei der Projekt-Kalkulation die Varianten-Kostenrechnung verwendet worden, hätten sich folgende Produktkosten ergeben:

Von Anfang an wäre sichtbar, dass sich die Gesamtkosten der Firma um 2.300€ erhöhen. Produkte 2+3 bleiben quasi unverändert, Produkt 1a wird tatsächlich etwas billiger, aber Produkt 1 erhöht sich signifikant, da ihm ein Teil der Stückzahl weggenommen wurde.
Diese Kalkulation zeigt damit eine ganz andere Möglichkeit zur Kosteneinsparung auf: Produkt 1a einführen und Produkt1 ganz aus dem Sortiment zu nehmen.
Mehr Hintergründe zur Variantenkostenrechnung
Einfache Ermittlung der Variantenkosten
In Business Cases werden üblicherweise alle Aufwendungen für die Entwicklung eines Produktes berücksichtigt, nicht jedoch die Kosten, die während des gesamten Lebenszyklus anfallen.
Die folgende Tabelle zeigt Aktivitäten während der typischen Lebensphasen eines Produktes. Obwohl es sich um zwei völlig unterschiedliche Firmen handelt, unterscheiden sich die Aktivitäten nicht prinzipiell. Die Methoden zur Ermittlung und Anwendung von Variantenkosten funktionieren also prinzipiell gleich.
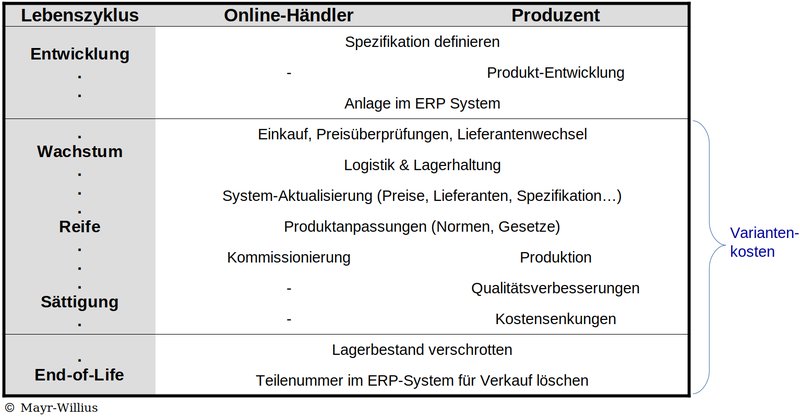
Um möglichst einfach in die schon verwendeten Kalkulations-Schemata eingefügt werden zu können, definieren wir hier als Variantenkosten alle Life-Cycle-Kosten jenseits der Entwicklungsaufwendungen. Also diejenigen Aufwände von Produkten und Bauteilen, die normalerweise nicht berücksichtigt werden.
Variantenkosten eines neuen Bauteiles werden oft durch zufällige Aktivitäten bestimmt. Deshalb macht es keinen Sinn, sie exakt buchhalterisch bestimmen zu wollen. Statt dessen ermitteln wir die Mittelwerte für Gruppen ähnlicher Teile und erstellen daraus einen Variantenkosten-Katalog. Um möglichst schnell dort zu Ergebnissen zu kommen, starten wir mit den Abteilungen und Bauteilen mit den größten Komplexitätsproblemen.
Interviews
Die Rohdaten der Variantenkosten gewinnen wir über Experten-Interviews innerhalb der untersuchten Abteilung. An Hand der Interviews ermitteln wir …
- die nötigen Aufgaben während des gesamten Lebenszyklus für die betrachteten Produkte,
- die dafür nötigen Resourcen und Ausgaben,
- Unterschiede in den Varianten, die deutlich unterschiedliche Belastungen aufweisen
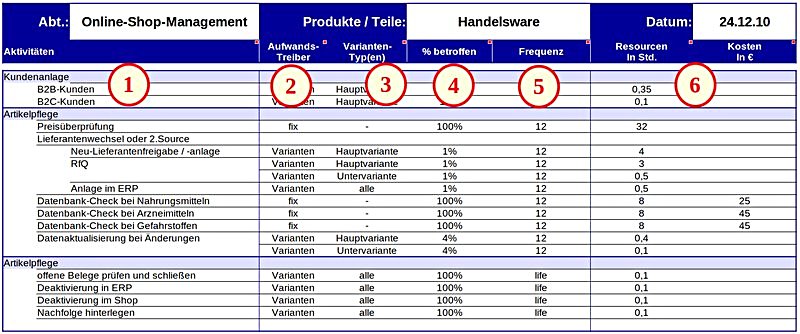
(1) Aktivitäten:
Die nötigen Aktivitäten listen wir so grob wie möglich und so detailliert wie nötig auf. Dabei berücksichtigen wir aber alle anfallenden Life-Cyle-Aufgaben , auch solche, die nur mit einer gewissen Wahrscheinlichkeit anfallen,zum Beispiel Anpassung an neue Normen oder nötige Qualitätsverbesserungen.
(2) Aufwand-Treiber:
Hier ermitteln wir welche Ursachen die Kosten der Aktivitäten bestimmen:
Fix: | immer gleicher Aufwand, unabhängig von Varianten oder Stückzahlen |
Varianten: | der Aufwand steigt mit der Anzahl der Varianten ist aber unabhängig von der Stückzahl |
Stückzahl: | der Aufwand steigt mit der Stückzahl, unabhängig von Varianten |
Falls mehr als nur ein Aufwandstreiber eine Aktivität bestimmt, zerlegen wir sie in Unteraktivitäten, bei denen wir die beiden Variantentreiber trennen können.
(3) Varianten-Typen
Als unterschiedliche Varaintentypen verstehen wir Varianten, die signifikant unterschiedliche Aufwände haben. Das sind zum einen Bauteile mit völlig unterschiedlichen Entwicklungsprozessen und zum anderen unterschiedliche Synergien mit anderen Bauteilen.
Zum Beispiel ist eine elektronische Steuerung sicher ein anderer Variantentyp als ein einfaches mechanisches Bauteil. Wenn wir aber von dieser Steuerung eine Bestückungsvariante ableiten, dann ist diese wieder ein eigener Variantentyp. Denn die Bestückungsvariante braucht nur einen Bruchteil des Aufwands verglichen mit der Hauptvariante.
(4) %-Anteil
Der %-Satz an betroffenen Varianten beschreibt, wie viele der Varianten von der Aktivität betroffen sind. Für Aufgaben, die jede Variante betreffen sind das 100%. Für Aufgaben, die nur einen Teil der Varianten betreffen , entsprechend diesem Anteil.
Der eCommerce-Manager eines Webshops führt zum Beispiel die Überprüfung der Stammdaten im monatlichen Rhythmus durch. Danach muss er im Schnitt 2% der Varianten aktualisieren. Dies entspricht dann folgenden Einträgen:
Überprüfung: Frequenz = 12 (monatlich), betroffene Teile = 100%
Aktualisierung: Frequenz = 12 (monatlich), betroffene Teile = 2%
(5) Frequenz
Die Frequenz beschreibt, wie oft im Jahr diese Aktivität für jede Variante durchgeführt werden muss. Bei monatlicher Wiederholung ist die Frequenz 12, bei 2jähriger Wiederholung nur 0.5 .
Bei zufällig auftretenden Aktivitäten, wie zum Beispiel normative Änderungen, verwenden wir einen Mittelwert über die letzten Jahre.
(6) Resourcen und Kosten
Hier tragen wir nun den nötigen Aufwand ein , der für die einmalige Aktivität bei einer Variante anfällt.
Die Freigabe einer neuen Elektronik erfordert zum Beispiel 500 Stunden, die für jede Elektronik für Labortests anfallen. Bestückungsvarianten dieser Elektronik werden als unterschiedlicher Variantentyp unterschieden. Hier fielen dann zum Beispiel nur 150Stunden ein eigenen Freigabetests an.
Aggregation zu Kennzahlen
Die Aggregationstabelle zeigt alle berücksichtigten Aufgaben (horizontal), die unterschiedlichen Kostentreiber (vertikal) sowie den zugehörigen Aufwand je Aufgabe und Variante. Außerdem wird noch die aktuelle Anzahl der entsprechenden Varianten eingetragen.
Damit können nun die Gesamtaufwände sowohl für jede Aufgabe (Resourcen-Auswertung, grüne Spalten rechts) wie auch für jeden Variantentyp (Variantenauswertung, grüne Zeile unten) ermittelt werden. Die nachfolgende Tabelle zeigt der Einfachheit halber nur die nötigen Arbeitsstunden, die Berechnung der Variantenkosten funktioniert jedoch genau gleich:
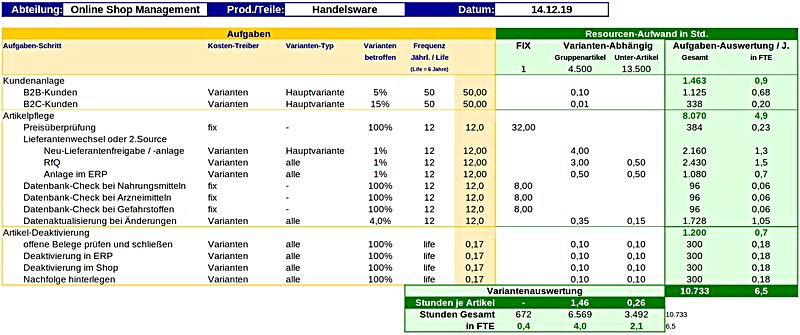
Zur besseren Nutzung vereinfachen wir die Varianten wenn möglich:
- Variantentypen, die in der Variantenauswertung sehr ähnliche Variantenkosten aufweisen, fassen wir zusammen
- Variantentpyen mit vernächlässigbar kleinen Aufwänden integrieren wir in andere Variantentypen.
Kalibrierung
Nachdem wir die Komplexitätskosten bis hierher bottom-up geschätzt haben, kalibrieren wir sie jetzt Top-Down:
- Gesamtresourcen und -budget: wie groß ist die Abweichung der Komplexitätskosten?
- Lassen sich die Abweichungen einzelnen Aufgaben zuordnen, die offensichtlich nicht mit der Realität übereinstimmen?
→ Markieren wir die entsprechenden Zeilen - Lassen sich die Abweichungen einzelnen Variantentreibern zuordnen?
→ Markieren der entsprechenden Spalten(n) - Sind Spalten und Zeilen markiert?
→ Anpassung der Schnittpunkte
→ Zurück zu (1) - Sind einzelne Spalten oder Zeilen markiert?
→ Prozentuale Anpassung aller Aufwände in den entsprechenden Zeilen/Spalten
→ zurück zu (1) - Keine Spalten oder Zeilen zeigen auffallende Abweichungen?
→ Prozentuale Kalibrierung aller Aufwände, so dass die Gesamt-Aufwände der aktuellen Abteilungssituation entspricht
Als Ergebnis erhalten Sie in (5) eine brauchbare Schätzung der nötigen Aufwände je Variante für die verschiedenen Variantentypen. Diese können Sie zur Kalkulation von Komplexitätsänderungen Ihrer Abteilung verwenden, also zum Beispiel um zu bestimmen, welche Resourcen sie für das geplante Variantenwachstum Ihres Webshops benötigen.
Zusammenfassung zum Variantenkosten-Katalog
Die ermittelten Variantenkosten der einzelnen Abteilungen fassen wir ein einem Variantenkosten-Katalog zusammen. Sobald die kritischsten Abteilungen aufgenommen sind, ist der Katalog für Business-Entscheidungen nutzbar. Dies könnte für einen Hersteller von Elektrogeräten folgendermaßen aussehen:
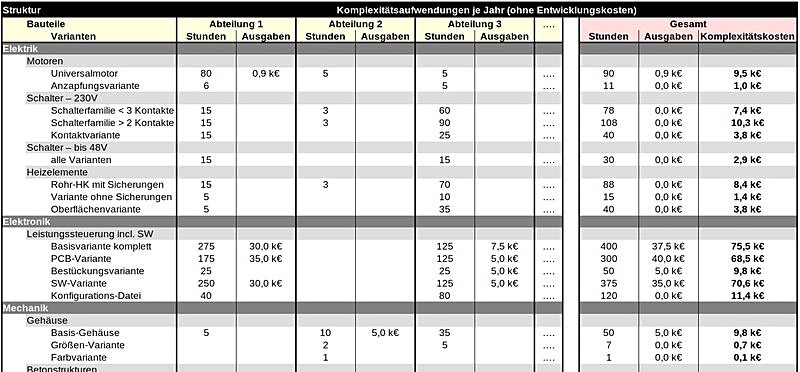
Für gleiche Bauteile und Variantentypen wird die Summe aller Abteilungs-Komplexitätskosten berechnet. Daraus ergeben sich dann die Gesamt-Komplexitätskosten, die für einen Business Case zur Anwendung kommen.
Bei den Abteilungen kann es sich z.B. um Entwicklung, Einkauf und Produktion handeln, oder aber auch um unterschiedliche Entwicklungsabteilungen Elektrik, Mechanik, Labor, …. , je nach Bereich für den die Komplexitätskosten verwendet werden sollen.
Die einfachste Ermittlung und Anwendung von Variantenkosten startet mit einigen wenigen kritischen Bereichen und Bauteilen. Danach wird der Katalog je nach Notwendigkeit ausgebaut.
Anwendung von Variantenkosten
Die folgenden typischen Beispiele zeigen, wie einfach und effizient ein Variantenkosten-Katalog angewandt werden kann. Falls Sie sich fragen, wie sie die Beispiele für Ihre Situation anpassen können, sprechen Sie mich unverbindlich an.
Variantenbasierte Budgetkalkulation
Schon nach der Analyse der ersten Abteilung können die ermittelten Variantenkosten für die langfristige Budgetplanung dieser Abteilung herangezogen werden.
Zum Beispiel in einem Web-Shop, der mit einem erweiterten Artikel-Angebot wachsen möchte. Hier hat die untersuchte Abteilung folgende Variantenkosten identifiziert:
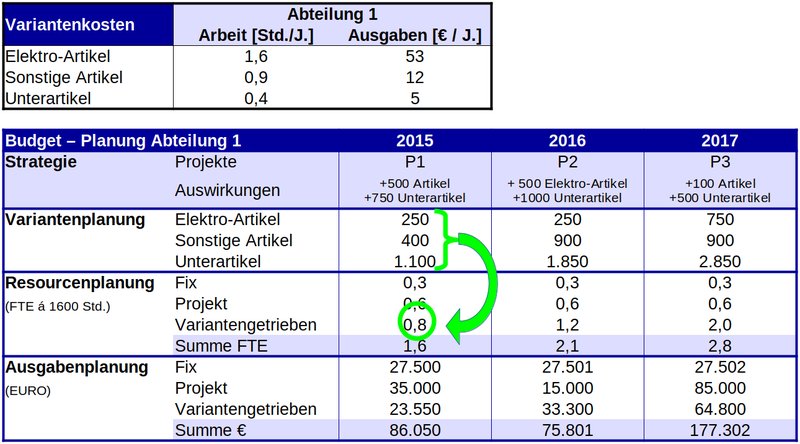
Für die Budgetplanung verwenden wir drei wesentlich unterschiedliche Kostentreiber,
- den fixen Aufwänden, unabhängig vom Projekten oder Varianten
- den Projektaufwänden, für eigens zu planende Aktivitäten außerhalb des Tagesgeschäfts
- den variantenabhängige Aufwänden, die von Produkt- und Teile-Komplexität abhängen.
Da wir aus dem Variantenkosten-Katalog die Aufwände für die unterschiedlichen Variantentypen kennen, lassen sich mit der Variantenplanung direkt die variantenabhängige Aufwände berechnen.
Ohne das Bewusstsein für die Wirkungsweise von Varianten würde das Budget vermutlich nicht an die höhere Komplexität angepasst. Damit wäre die Abteilung bald nicht mehr in der Lage, alle Aktualisierungsaufgaben mit der nötigen Sorgfalt zu erledigen, die Qualität des Shops würde deutlich abnehmen.
Analog zum obigen Beispiel kann dieser Ansatz für jede Abteilung angewandt werden. Es ändern sich nur jeweils die Variantentypen und ihre Komplexitätskosten.
Kosteneinsparungen mit Varianten
Im typischen Produktlebenszyklus (siehe auch Online Lehrbuch BWL) beginnt mit der Reife-Phase die verstärkte Konzentration auf Kosteneinsparungen.
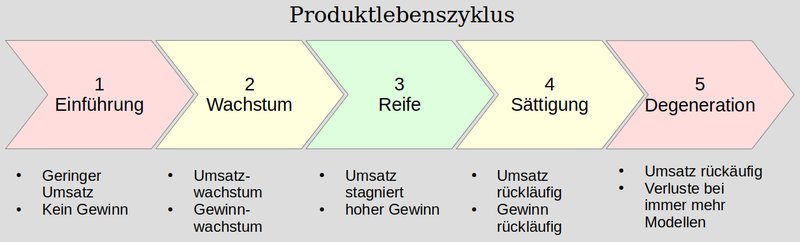
Eine beliebte Möglichkeit besteht darin, aus Bauteilen mit einem großen Funktionsumfang, billigere mit weniger Funktionen zu entwickeln.
Dadurch wird jedoch die Komplexität erhöht, mit der Gefahr, dass
- die sich die geplanten Kosteneinsparungen nicht in der Bilanz niederschlagen.
- die Organisation sich immer mehr mit den Varianten herumschlägt und unflexibel wird.
Aber gerade in der Reife- und Sättigungsphase ist eine schnelle Anpassung an Kundenanforderungen wichtig, und dazu gehören auch neue Varianten. Die Ermittlung und Anwendung von Variantenkosten hilft, die „guten Varianten“ von den unrentablen zu unterscheiden.
Business-Case ohne Variantenkosten
Szenario: Für eine elektronische Steuerung sollen Sie eine neue Variante optimieren, indem Sie eine Funktion eliminieren, die im unteren Preissegment unwichtig ist. Die kostenoptimierte Lösung sieht ein Re-Design vor, mit Streichung eines Relais, Verwendung eines kleineren Prozessors und Verkleinerter Leiterplatte. Eine erste Schätzung geht von jährlichen Ersparnissen von ca. 130.000 € aus (Alternative 1).
Als Alternativ-Konzept (Alternative 2) wurde vorgeschlagen, das Design beizubehalten und nur das Relais nicht zu bestücken. Die jährliche Ersparnis wäre dann aber nur ca. 63.000€
Auf den ersten Blick sieht die Alternative des vollständigen Re-Designs attraktiver aus:
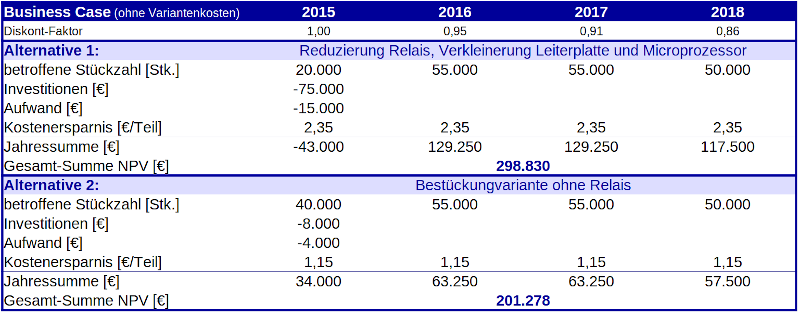
- Stückzahl: die von der Umstellung betroffen Stückzahl, im ersten Jahr niedriger durch den Projektstart, ab 2018 abfallend.
- Investitionen & Aufwand: nötige Werkzeugänderungen wie auch die Re-Design- und Freigabeaufwände
- Kostenersparnis: Bei Re-Design (Alternative 1) würden die Kosten um 2,35€ gesenkt, bei der Bestückungsvariante (Alternative 2) nur 1,15€ je Teil
- NPV (Net Present Value) ist die Gesamtersparnis über alle Jahre. Alternative 1 hat mit fast 300.000€ die größte Ersparnis. Die Ergebnisse der unterschiedlichen Jahre werden hier auf das Startjahr umgerechnet um zeitlich unterschiedliche Geldflüsse vergleichbar zu machen. Siehe hierzu die Erklärungen zu NPV und Diskontierung.
Business-Case mit Variantenkosten
Mit Alternative 1 würde ein völlig neues Design eingeführt. Dies erfordert ein eigenes Qualitätsmanagement sowie den kompletten Verbesserungs- und Freigabeaufwand bei Änderungen. Aus unserem Variantenkosten-Katalog entnehmen wir, dass die gesamten Variantenkosten dafür bei ca. 75.500€ / Jahr liegen.
Alternative 2, bei der nur die Bestückung des Relais geändert würde, hätte nur einen geringen Variantenaufwand. Der besteht hauptsächlich aus Dokumentation, da alle Verbesserungs- und Freigabe-Aktivitäten weiterhin für die Hauptelektronik erledigt werden. Die Variantenkosten für eine Bestückungsvariante stehen mit ca. 9.800€ / Jahr im Katalog.
Nach Berücksichtigung der Komplexitätskosten im Business Case erscheint jetzt Alternative 2 die wesentlich rentablere Lösung.:
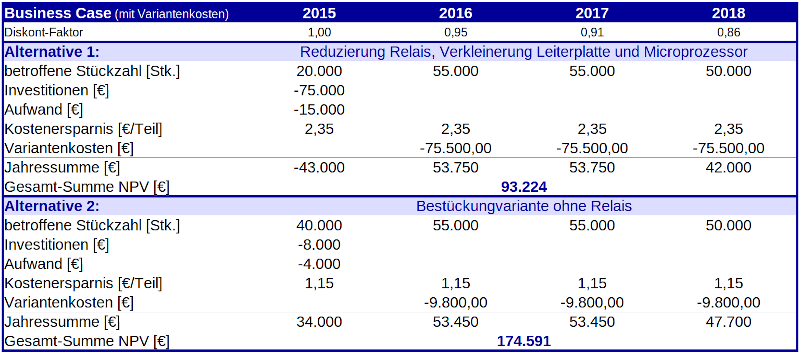
Fazit
Durch die Berücksichtigung der Komplexitätskosten können Sie unrentable Projekte vermeiden, bei denen Einsparungen durch die höhere Komplexität zunichte gemacht würden.
Jedoch ist nicht jede Komplexität schädlich. Deshalb beruht eine korrekte Ermittlung und Anwendung von Variantenkosten darauf, dass unterschiedliche Variantentypen identifiziert und unterschieden werden.
Variantenoptimierung einer ganzen Bauteil-Familie
Szenario: Sie sollen für eine gesamte Produktfamilie eine entsprechende Baureihe an Elektromotoren entwickeln. Aus den Produktanforderungen ergeben sich die folgenden Anforderungen an die Motoren:

Da alle Motoren die gleichen Endschilde und Wicklungsbleche besitzen, fallen nur einmalige Investitionen an, unabhängig von der Anzahl der Motorvarianten.
Da Motoren jedoch sicherheitsrelevant sind, ergeben sich für jede Variante relativ hohe Variantenkosten, weshalb wir schädliche Komplexität vermeiden wollen.
Die beiden extremen Lösungen
Die beiden widersprüchlichen Forderungen, zum Einen nach minimalen Kosten, zum Anderen nach minimaler Komplexität, ergäben extrem unterschiedliche Lösungen
- niedrigste Materialkosten → ein genau zugeschnittener Motor für jedes Segment
- niedrigste Komplexitätskosten → ein einziger Standard-Motor, der alle Segmente abdeckt
Beide Lösungen sind viel zu ineffizient und das Optimum liegt vermutlich irgendwo dazwischen. Aber die beiden Extreme ergeben unterschiedliche Startpunkt für die Ermittlung des Variantenoptimums:
Variantenanzahl reduzieren
Wir beginnen mit der auf niedrige Materialkosten getrimmten Lösung. Jedes Marktsegment erhält seinen exakt zugeschnittenen Motor, für den wir die Spezifikation anpassen und beim Hersteller die Preise nachfragen:
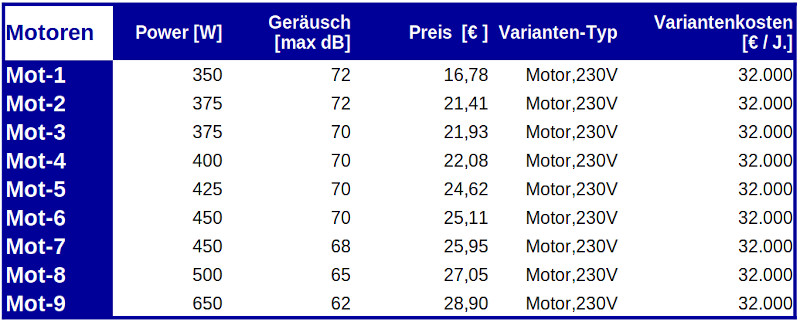
Um die optimale Variantenanzahl zu ermitteln, eliminieren wir schrittweise die unrentablen Motoren:
- Für jeden Motor berechnen wir die möglichen Einsparungen, wenn er vom nächst größeren Motor ersetzt würde (wir nehmen also höhere Materialkosten in Kauf, um Variantenkosten einzusparen):
Kostendifferenz (i) = Preisdifferenz (i, i+1) * Stückzahl (i) – Variantenkosten (i) - Den Motor mit den größten Einsparungen ersetzen wir dann
- und wiederholen diese Schritte solange, bis keine Einsparungen mehr möglich sind
Diese Schritte können ohne weiteres in einer Tabellenkalkulation durchgeführt werden:
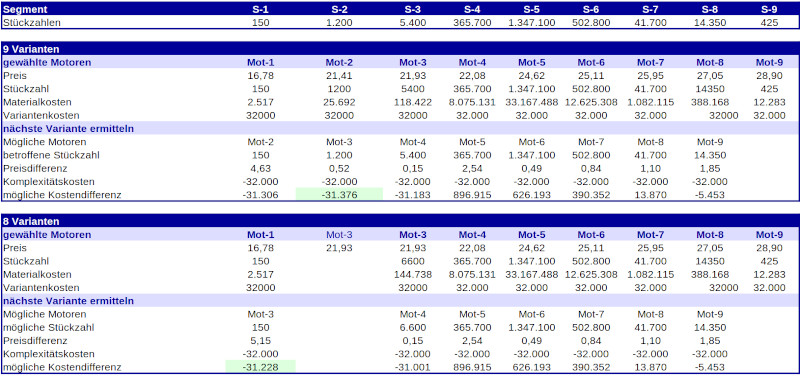
Im obersten Block befinden sich die Produktsegmente mit ihren Stückzahlen. Darunter die Kalkulation für alle Motorvarianten. Im oberen Teil die Material- und Variantenkosten, darunter die Kosten, die sich ergäben, falls der entsprechende Motor vom nächst größeren ersetzt würde. Hier sollte Mot-2 durch Mot-3 ersetzt werden, da die größte Ersparnis winkt (wir sparen die Variantenkosten von ca. 32.000€ bei erhöhten Materialkosten von 624€)
Der Block darunter beschreibt nun die Situation, nachem Mot-2 durch Mot-3 ersetzt wurde. Der nächste zu ersetzende Motor wäre jetzt Mot-1, der durch Mot-3 ersetzt werden kann.
Wenn wir diese Schritte weiterführen, erhalten wir ein Optimum von 5 Varianten, nämlich die Motoren 4-5-6-7-9.
Variantenanzahl erhöhen
Wir können die Variantenoptimierung auch mit der niedrigsten Komplexität starten, dem Standardmotor, der alle Segmente abdeckt. Danach fügen wir Schritt für Schritt denjenigen Motor hinzu, der die größten Einsparungen aufweist.
- Für jeden noch nicht verwendeten Motor berechnen wir die möglichen Einsparung durch seinen Einsatz (wir reduzieren so die Materialkosten indem wir die Variantenkosten erhöhen):
Kostendifferenz (i) = Preisdifferenz (i, n) * Stückzahl (i) – Variantenkosten (i) - Den Motor mit den größten Einsparungen fügen wir ein
- und wiederholen diese Schritte solange, bis keine Einsparungen mehr möglich sind
Die Lösung mit Tabellenkalkulation sieht wieder ganz ähnlich aus:
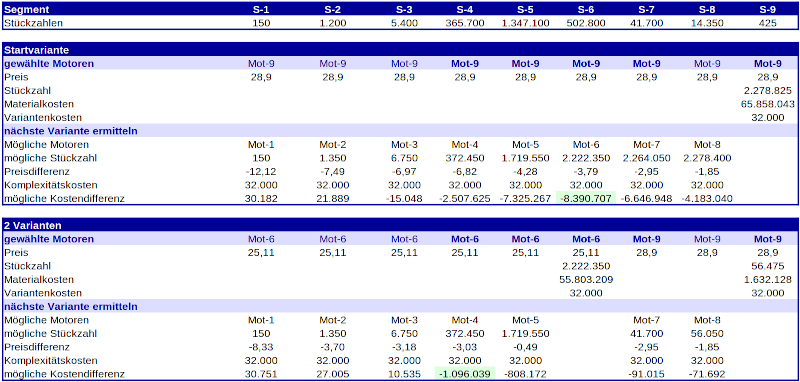
Der oberste Block zeigt wieder Segmente und Stückzahlen, darunter kommt die Kalkulation für den Fall des einen Standardmotors Mot-9. Im oberen Teil werden wieder Material- und Variantenkosten berechnet, darunter die Kosten, die sich ergäben, wenn man den jeweiligen Motor zusätzlich einsetzen würde. Hier sollte nun Mot-6 eingeführt werden, da er eine Gesamtersparnis von über 8Mio € erzielen würde, v.a. basierend auf den doch deutlich niedrigeren Teilekosten gegenüber Mot-9.
Der Block darunter beschreibt nun die Situation, nachdem Mot-6 eingeführt wurde. Der nächste einzuführende Motor wäre jetzt Mot-4.
Wenn wir diese Schritte weiterführen, erhalten wir das gleiche Variantenoptimum wie oben.
Optimale Variantenanzahl
Die Ergebnisse der beiden Herangehensweisen können in der folgenden Grafik zusammengefasst werden, die sehr schön zeigt, dass
- bei hoher Variantenanzahl die Zunahme der Variantenkosten dominiert
- bei zu niedriger Variantenanzahl die Materialkosten regelrecht explodieren
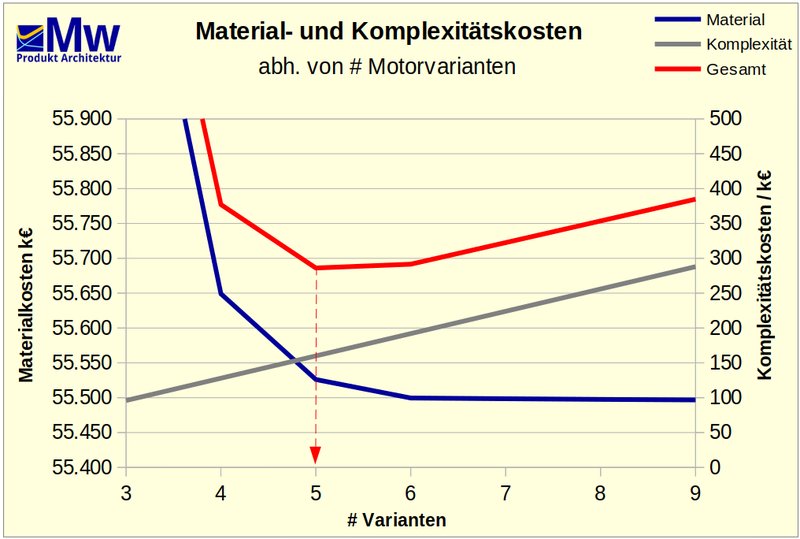
Das Optimum liegt meist zwischen den beiden Extremen, abhängig von den Preis- und Stückzahl-Profil.
Der Anschaulichkeit halber wurde das obige Beispiel ein wenig vereinfacht. In der Realität kosten die meisten Varianten zusätzliche Investitionen und Entwicklungskosten. Diese können in der Kalkulation oben ähnlich berücksichtigt werden wie die Variantenkosten, aber natürlich nur mit ihrem jährlichen Anteil.
Desweiteren bietet eine niedrigere Variantenanzahl natürlich auch Verhandlungsoptionen mit den Zulieferern, da diese nun je Variante deutlich höhere Stückzahlen bekommen.
Bei vielen Bauteilen existiert nicht nur ein Variantentyp sondern mehrere (wie im obigen Elektronikbeispiel eine Haupt- und eine Bestückungsvariante). In diesem Fall führen wir die Variantenoptimierung zweistufig durch, zuerst mit den Hauptvarianten (mit den hohen Variantenkosten), und von diesem Zwischenoptimum aus mit den Untervarianten.
Die gezeigte Methode funktioniert auch bei Bauteilen, die nicht mehr einfach durch die jeweils nächsthöhere Variante ersetzbar sind. In diesem Falle schalten wir der Kalkulation eine Ersetzungmatrix vor, die bestimmt, welche Variante durch welche andere(n) ersetzt werden kann.
Komplexitätsreduktion schon bestehender Varianten
Auch wenn die Variantenoptimierung natürlich am effektivsten ist, bevor „unnötige“ Varianten entwickelt wurden, lassen sich auch bestehende Bauteil-Reihen rentabel optimieren. Dies wird immer dann interessant, wenn sich mit der Zeit die Stückzahlen zwischen den Varianten deutlich verschoben haben.
Die oben gezeigten Kalkulationen bleiben weitgehend die gleichen: Wir vergleichen die gesparten Materialkosten mit den zusätzlichen Variantenkosten, allerdings mit dem Unterschied, dass
- Entwicklungskosten und -investitionen nicht mehr berücksichtigt werden, denn diese sind ja schon ausgegeben.
- Überzählige Varianten nicht sofort ersetzt werden, denn sie sparen ja tatsächlich Materialkosten, sondern „eingefroren“ werden.
Das „Einfrieren“ zu eliminierender Varianten bedeutet, dass sie nicht mehr bearbeitet werden, für sie also keine Variantenkosten mehr anfallen. Bei Auftreten der ersten Problemen werden sie ersetzt, und so lange wird noch ihre Kostenersparnis genutzt.
Um das Einfrieren und Elimineren auch wirklich sicherzustellen und an alle betroffenen Abteilungen zu kommunizieren, bietet sich eine Bauteile-Roadmap an, die für jede Variante die geplante Weiterentwicklung darstellt:
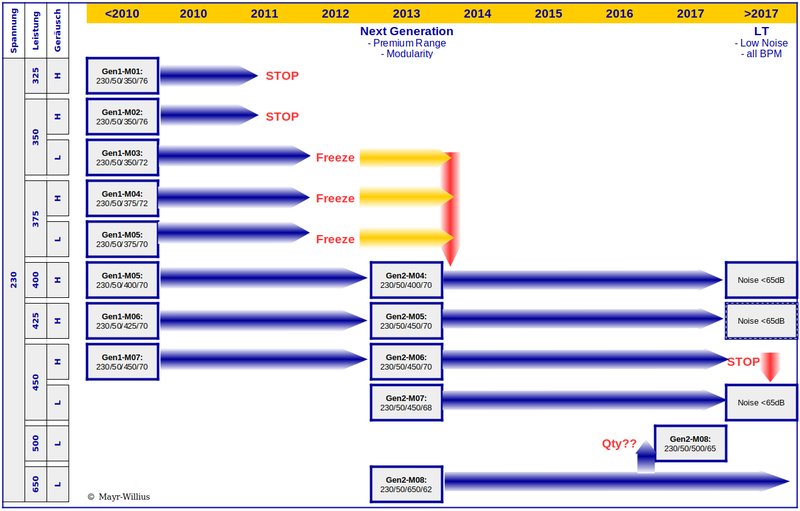
Unterstützende Organisation
Die Ermittlung und Anwendung von Variantenkosten kann mit den kritischen Bereichen starten und dann Schritt für Schritt ausgeweitet werden. Richtig effektiv jedoch werden sie, wenn sie durch entsprechende organisatorische Strukturen unterstützt werden. Der erste Schritt hierzu ist die Definition entsprechender Rollen, Befugnisse und Verantwortlichkeiten.
Modul-Architekt:in
Die meisten Aufgaben zur Ermittlung und Anwendung von Variantenkosten befassen sich mit der gesamten Bauteilfamilie, also der gesamten Variantenstruktur des Bauteiles. Deshalb ist die erste wichtige Rolle die eine:r „Modul-Architekt:in“.
- Das Modul bezeichnet das „imaginäre Bauteil“, das die gesamte Bauteilfamilie repräsentiert und die Gemeinsamkeiten der Varianten in sich trägt, z.B. die Schnittstellen und Kernfunktionen (siehe „Modulare Produktarchitektur“ )
- Als „Architekt:in“ bezeichnen wir die Rolle, weil sie sich auf die Struktur und das Zusammenspiel der Teile konzentriert, wie eben der bekannte Architekt beim Haus.
Wichtige Aufgaben dieser Rolle sind
- Definition einer Modulstruktur mit einheitlichen Schnittstellen für das betrachtete Modul (denn nur bei gleichen Schnittstellen lassen sich die Varianten überhaupt austauschen wie oben beschrieben)
- Definition der Variantentypen
- Ermittlung und Bewertung der Life-Cycle-Aufgaben für das betrachtete Modul, so dass daraus die Variantenkosten (Resourcen & Ausgaben) bestimmt werden können.
- Erstellen einer optimalen Variantenstruktur bei Produktstart und auch zur Erfüllung veränderter Produktanforderungen
- Überprüfung und Anpassung der Variantenstruktur sobald sich Preise und Stückzahlen signifikant verändern
- Erstellen und umsetzen einer Modul-Roadmap, die u.A. die Einführung bzw. Beendigung von Varianten plant, kommuniziert und umsetzt.
Produkt-Architekt:in
Ein:e Modul-Architekt:in kann erst wirklich etwas bewirken, wenn auch auf Produktebene in Familien und Varianten gedacht wird, wenn es also ein:e Produkt-Architekt:in gibt.
Wichtige Aufgaben sind
- Erstellen und weiterentwickeln einer gesamten Produktstruktur, also der Gesamtheit der benötigten Modules, so dass diese abgestimmte und passende Schnittstellen besitzen
- Erstellen des gesamten Variantenkosten-Katalogs
- Weiterentwicklung der Produktarchitektur bez. Qualität, Kosten und Performance, wobei bei den Kosten immer die Variantenkosten berücksichtigt werden.
- Erstellen und umsetzen einer Produkt-Roadmap in Abstimmung mit anderen Abteilungen und den Modul-Roadmaps
Siehe auch „Komplexitätsmanagement“
Fazit
Sie wissen um die Problematik, Ihren Kunden exakt zugeschnittene Produkte anzubieten und gleichzeitig weder Kosten noch Komplexität zu erhöhen. Dabei ist weder die sture Standardisierung, noch die unbegrenzte Entwicklung neuer Varianten eine gute Lösung. Die Nutzung eines Variantenkosten-Katalogs bietet hier einen Ausweg.
Ein Variantenkosten-Katalogs kann schrittweise erstellt und seine Anwendung leicht in die aktuellen Abläufe integriert werden. Starten Sie mit den Komponenten und Abteilungen, die am kritischsten sind, und erweitern Sie den Katalog nach Notwendigkeit. Gerne unterstütze ich Sie dabei, sprechen Sie mich einfach unverbindlich an .
Die Anwendung von Variantenkosten läßt sich am zuverlässigsten durch die Definition entsprechender Verantwortlichkeiten einführen. Ob zur Entwicklung einer ganze Baureihe oder bei Kosteneinsparungen, auch hier können Sie parallel zum Katalog Schritt für Schritt vorgehen.
Die möglichen Einsparungen sind natürlich umso größer, je modularer Ihre Produktstruktur ist. Diese hat noch weitere positive Effekte, mehr darüber finden Sie unter